More than 80 years of expert guidance for your projects
As the leading contract development and manufacturing organization (CDMO), DPT, a Mylan company, is recognized for our expertise in semi-solid and liquid dosage forms, with an established legacy of excellence dating back more than 80 years.
More than any other CDMO, we understand how scale-up will be interwoven into full-scale commercialization from your research and development project. From pre-formulation to commercial manufacturing, you only need one partner to streamline your path from lab to market: DPT does it all.
You won’t have to look far for measures of success — the proof is in every product.
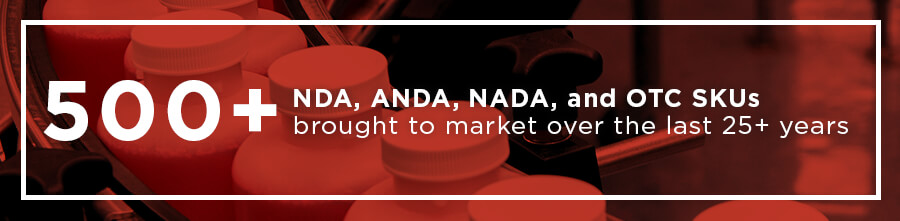
Quality: Quantified at DPT
Quality underlies everything we do at DPT. Our quality control and quality assurance specialists play a key role at every step, and we manufacture everything to the latest cGMP standards, but there’s more to it than that. Everyone at DPT is committed to incorporating quality into every aspect of our jobs — and you can see it in every product we make.